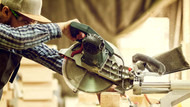
Dec 9th 2024 |
Guide to Managing Carpentry Safety in Australia: Understanding the Australian Standards for Carpentry
Carpentry is a cornerstone of the Australian construction industry, playing a pivotal role in shaping homes, commercial buildings, and infrastructure. The demand for carpenters and joiners continues to rise in Australia, with a projected job growth of 11.7% by 2024. This calls for the crucial prioritising of woodworking safety. The construction industry, expected to grow at 6.8% annually over the next five years, presents exciting opportunities and potential hazards. Here, we will provide you with a guide to managing woodworking safety in Australia.
What is Carpentry?
Carpentry involves cutting, shaping, and installing building materials to construct and finish structures. Carpenters are integral to creating the frameworks of buildings, concrete formwork, and structural timber components. Their work supports various construction projects, from residential homes to large-scale commercial developments.
Modern carpentry is governed by strict Australian standards and guidelines to ensure safety and quality. The Australian Building Codes Board maintains the National Construction Code, which sets out technical provisions for building design and construction. Carpenters must adhere to these standards to ensure compliance and safety on worksites.
What is Considered as Carpentry Work?
Carpentry work encompasses a wide range of tasks and responsibilities. Here are some examples:
- Constructing and installing wooden structures such as walls, roofs, floors, and partitions.
- Building and installing wooden frameworks for doors, windows, and cabinetry.
- Installing and fitting wooden fixtures, including skirting boards, architraves, and mouldings.
- Assembling and installing prefabricated wooden components in construction projects.
- Working with timber to create furniture, joinery, and decorative elements.
- Repairing and renovating wooden structures, including fixing damaged or deteriorated sections.
- Using various hand and power tools, such as saws, drills, chisels, and planes, to shape and manipulate wood.
- Operating woodworking machinery, such as routers, planers, and sanders, to refine wooden surfaces.
Crafting furniture and structures requires strenuous effort, demanding immense strength and stamina from carpenters. A carpenter may spend long hours standing, bending, and lifting heavy materials. They must also be able to work in various environments, from dusty construction sites to clean, climate-controlled workshops.
Hazards in Carpentry Work
Carpentry work presents a variety of hazards that can cause severe injury or even death. Here are some of the most common risks associated with carpentry:
- Wood dust: In Australia, all wood dust is now classified as carcinogenic (liable to cause cancer). Wood dust exposure can lead to respiratory problems like asthma, bronchitis, and cancer.
- Chemicals: Chemicals used in the woodworking industry can also threaten workers' health. These chemicals include solvents, adhesives, and preservatives.
- Machinery: The machinery used in woodworking can be dangerous if not used properly. Workers can suffer from cuts, lacerations, and amputations if they come into contact with the machinery.
- Falls: Falls are the foremost cause of mortality in construction. Carpenters often work at heights, whether it be on ladders, scaffolding, or roofs.
- Toxic timbers: Some timbers used in woodworking can be poisonous and cause skin irritation, respiratory problems, and other health issues.
- Electrocution: Carpenters work with power tools and electrical wiring, which can be dangerous if incorrectly handled.
- Spinning blades: Working with saws and other power tools can be dangerous due to the high-speed spinning and sharp blades.
Australian Compliance Framework for Woodworking and National Construction Code
Due to the risks associated with working with timber, carpenters must know the relevant guidelines and Australian standards, which are crucial in ensuring compliance with safety and construction practices. Carpenters must be familiar with them, and employers should also ensure that workers comply with these regulations and standards to keep the workplace safe. The National Construction Code (NCC) sets minimum requirements for building design and construction, including fire safety, accessibility, sustainability, and plumbing in Australia. Here are some of the Australian Guidelines related to woodworking safety rules and the industry:
AS/NZS 4785.3:2002
AS/NZS 4785.3:2002 specifies the necessary product requirements and grade descriptions for sawn and milled softwood timber used in furniture components throughout Australia. The standard includes moisture content, tolerances, and grade descriptions for softwood timber used in furniture components.
AS 1473-1991
AS 1473-1991, developed by Standards Australia, focuses on guarding and safely using woodworking machinery and hand tools. It establishes guidelines and minimum requirements to ensure operator safety equipment, manufacturer, supplier, employer, and user safety when cutting or abrading wood and similar materials.
Guidance Note - Safe Use of Woodworking Machinery (Guarding)
The Guidance Note - Safe Use of Woodworking Machinery (Guarding) is a document WorkSafe Western Australia Commission developed. This note offers crucial information to ensure the safety and well-being of all those working with woodworking machinery. Whether operating, cleaning, replacing blades, or repairing equipment, it's essential to take necessary precautions to prevent accidents and maintain a healthy work environment.
Carpentry Australia Code of Conduct
The Carpentry Australia Code of Conduct is a set of guidelines that defines the benchmark standards for the carpentry industry in Australia. It is the only trade-based organisation dedicated to carpentry and carpenters in Australia, providing support for every qualified and apprenticed carpenter.
Risk Management in Woodworking
Compliance with Australian regulations safety rules and guidelines is insufficient to ensure a safe working environment. Implementing risk management strategies to reduce workplace hazards in the woodworking industry is also necessary. Risk management is the process of identifying potential hazards, assessing the risks associated with those hazards, and implementing measures to minimise or eliminate them.
Additionally, having comprehensive knowledge and ongoing training in the latest safety protocols and regulations is crucial for promoting safety standards and ensuring a safe working environment for carpenters.
1. Identifying Potential Hazards
The first step in risk management is identifying potential hazards in the environment. These hazards include sharp tools, heavy machinery, flammable materials, and ergonomic issues. Conducting a thorough assessment of the workspace and the tasks involved will help identify these hazards.
2. Assessing Risks
Once the hazards are identified, the next step is to assess the risks associated with each danger. This involves evaluating an accident's likelihood and potential severity consequences. For example, a sharp tool may present a risk of minor injury if not stored properly.
3. Implementing Safety Measures
It is essential to implement appropriate safety measures to mitigate risks. This can include creating safety policies and procedures, providing adequate training to woodworkers, and ensuring compliance with relevant safety standards and regulations. In non-cyclonic areas, specific safety measures are outlined in Australian and New Zealand construction standards for residential timber-framed construction. Here are some other safety measures that you should take:
- Personal Protective Equipment (PPE): Personal Protective Equipment (PPE) is crucial in minimising the risks associated with woodworking. Carpenters should wear appropriate PPE, such as safety goggles, gloves, ear protection, and respiratory masks, to protect themselves from potential injuries or exposure to harmful substances.
- Training and Education: Proper training and education are vital for carpenters to understand the risks and how to mitigate them effectively. Carpenters should receive comprehensive training on safe woodworking practices, including the proper use of tools and machinery, material handling techniques, and emergency procedures. This can include educating workers with the following:
- Safe Use of Tools: Tools can be dangerous if not used properly. Carpenters should adhere to manufacturer instructions and safety guidelines when using tools. This includes maintaining sharp and well-maintained blades, securing workpieces firmly, and using appropriate guards and safety features.
- Proper Material Handling: Safely handling materials is crucial to minimise the risk of accidents. Carpenters should use proper lifting techniques, ensure clear pathways, and store materials securely to prevent tripping hazards and material damage.
- Fire Safety Precautions: Working with timber products involves using flammable materials, making fire safety precautions essential. Carpenters should have fire extinguishers readily available, maintain a clutter-free workspace, and follow proper storage and disposal procedures for flammable substances.
- Emergency Preparedness: Despite taking preventive measures, emergencies can still occur. Carpenters should have an emergency plan, including procedures for handling injuries, contacting emergency services, and evacuating the premises if necessary. Regular drills and training sessions help ensure preparedness.
- Maintaining a Clean and Organised Workspace:
- A clean and organised workspace is visually appealing and contributes to safety. Keeping the workspace tidy reduces the risk of accidents caused by slips, trips, and falls. It also facilitates efficient workflow and minimises distractions.
- Regular Equipment Maintenance: Maintaining tools and machinery ensures their safe and optimal functioning. Carpenters should follow manufacturer recommendations for maintenance, including cleaning, lubrication, and equipment inspection.
4. Hazard Reporting and Incident Investigation
Carpenters should actively participate in hazard reporting and incident investigation processes. Reporting potential hazards allows for timely mitigation while investigating incidents helps identify root causes and implement preventive measures. All workers should feel encouraged and supported when reporting any safety concerns.
5. Utilising Safety Documents
Creating safety documents, such as safe work method statements or safety hazard and risk management plans, can help document safety measures and monitor compliance. These documents should be accessible to all relevant employees and regularly reviewed to ensure their continued relevance.
Documents for Managing Safety in Carpentry
There are documents that you can use to document your practices. They assist you in managing safety in carpentry. These documents include the following:
Safe Work Method Statements (SWMS)
An SWMS is a document that outlines the high-risk construction work activities involved in carpentry and the associated hazards and control measures. It includes step-by-step safety procedures for carrying out the work safely, identifies potential risks, and specifies the required personal protective equipment (PPE). An SWMS must be prepared for high-risk construction work and communicated to all relevant workers.
Integrated Management System for Carpentry
An Integrated Management System (IMS) for Carpentry combines a business's systems, processes, and standards, uniting them under one comprehensive framework. This system allows managing similar operations across health, safety, environment, and quality without duplication. An IMS enables an organisation to function as a cohesive unit with unified objectives, which cannot be achieved with individual management systems.
Work Health and Safety Policy
A work health and safety policy is a document that sets out the carpentry business's commitment to health and safety. It defines the responsibilities and accountabilities of management, supervisors, and workers in ensuring a safe working environment. The policy should align with the relevant legislation and regulations in Australia.
Construction Induction Card (White Card)
A White Card, also known as a Construction Induction Card, is mandatory for all workers involved in construction work in Australia, including carpentry. It is obtained after completing the General Construction Induction Training, which covers essential health and safety information for construction sites. Workers must carry and present their White Card on-site as proof of completion of the training.
Incident and Hazard Reporting Forms
Incident and hazard reporting forms document incidents, accidents, near misses, or hazardous situations on the site. These forms capture essential details such as the date, time, location, individuals involved, description of the incident, and any immediate actions taken. Reporting incidents and hazards promptly helps identify trends, implement corrective actions, and prevent future incidents.
Asbestos Register
Asbestos is a hazardous material that may be present in older buildings and construction sites. In Australia, it is crucial to maintain an asbestos register that documents the identification, location, and condition of any known or suspected asbestos-containing materials. Carpenters should be aware of the risks associated with asbestos and follow safe work practices when working in areas where asbestos is present.
Manual Handling Risk Assessment
Carpenters often engage in manual handling tasks that involve lifting, carrying, and moving heavy objects. The purpose of manual handling risk assessment is to identify potential ergonomic hazards and develop control measures to minimise the risk of musculoskeletal injuries. The evaluation should consider factors such as load weight, repetitive tasks, awkward postures, and the availability of mechanical aids or assistance.
Toolbox Talks
Toolbox talks are short safety meetings held regularly on the carpentry site to discuss specific safety topics, share information, and reinforce safe work practices. These talks promote safety awareness, address emerging issues, and encourage open communication among workers. Topics can include ladder and safety tips, power tool usage, working at heights, and other relevant carpentry-specific hazards.
Emergency Response Plan
An emergency response plan outlines the procedures to be followed, such as a fire or medical emergency. It should include information on evacuation routes, emergency contacts, first aid equipment and supplies, and contact details for authorities. You must review the plan periodically to ensure it is up-to-date and relevant.
Complete your Risk Management With SafetyDocs
Are you looking for a comprehensive range of carpentry safety documents? SafetyDocs by SafetyCulture offers safety documents tailored to your team's well-being. Our experienced experts have developed these resources to cover all aspects of workplace safety, from management plans to risk assessments and method statements.
With SafetyDocs, you can get your safety documents quickly. These tools are more than just paper; they are your guides to a safer work environment. Browse our library of carpentry-specific safety documents:
- Carpentry on Construction Safe Work Method Statements Pack
- Carpenters HSEQ Management System for New Zealand
- Builders Safe Work Method Statements Pack
Contact us today to learn how SafetyDocs can help establish a safety culture in your carpentry workplace. Let's build a future where craftsmanship and safety go hand in hand.
Our team of experts is dedicated to providing accurate and informative content. Craig Cruickshank, our senior HSEQ advisor at SafetyDocs by SafetyCulture has reviewed this blog post to ensure the highest level of quality.
Learn more about Craig's work on LinkedIn for more industry insights.
Available for instant download and supplied in fully editable MS Word format for use in your business.
Please note that the above information is provided as a comment only and should not be relied on as professional, legal or financial advice.
Share This Article