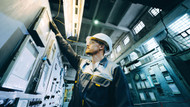
Apr 24th 2024 |
Managing the Risks of Plant in the Workplace: An Essential Guide to Australian Compliance
Plant and equipment form the backbone of countless Australian industries. From heavy-duty machinery in mining and construction to specialised tools in manufacturing and agriculture, plant enable productivity and efficiency. However, when not managed effectively, plant poses significant risks to worker safety.
This danger is highlighted by incidents such as forklift rollovers, worker entanglement, and equipment failures. Injuries and fatalities caused by these incidents remain a serious concern nationwide, emphasising the crucial need for proactive and robust safety measures.
Australian workplaces are governed by the Work Health and Safety (WHS) Act and associated regulations. These and the Code of Practice: Managing the Risks of Plant in the Workplace provide a framework for employers to ensure safe plant practices. This guide explores essential aspects of plant safety in the Australian workplace, empowering you to implement effective systems to safeguard workers and achieve compliance.
Definition of Plant and Equipment
In the world of workplace safety, the term 'plant' encompasses a wide range of machinery and equipment used in various industries. Here's a breakdown of typical categories:
- Mobile plant: Vehicles, earthmoving equipment, cranes, elevating work platforms (EWPs), forklifts, and other mobile machinery.
- Fixed plant: Generators, compressors, conveyor systems, manufacturing machinery, and similar stationary plant.
- Powered tools: Handheld or portable tools powered by electricity, pneumatics, hydraulics, fuel, or cartridges (e.g., drills, grinders, saws, nail guns).
- Amusement devices: Carnival rides, inflatables, and other similar devices used for entertainment.
Plant vs. Tools: Understanding the Distinction
While both plant and tools are used to perform tasks, the key difference lies in scale, potential risk, and regulatory requirements. Plant generally poses a higher risk of severe injuries due to its size, power, and complex moving parts. As such, there are often specific licensing, competency, and operational requirements surrounding this type of machinery, which might not apply to smaller, handheld tools.
Key Areas in Plant Safety Management
1. Purchase and Hiring
Before introducing any new plant to the workplace, conducting thorough risk assessments is crucial. Key Considerations include:
- Suitability: Is the equipment designed for the intended tasks and working environment?
- Safety features: Does it have necessary guards, emergency stops, and other safety mechanisms?
- Maintenance requirements: What are the manufacturer's maintenance and inspection recommendations?
- Operator training: What skills and competencies are needed for safe operation?
2. Identification of Equipment
A robust system for identifying and tracking plant is essential for safety management. Here's why:
- Clear Records: A register should log each item of plant, including identification numbers, safe working loads, inspection dates, and maintenance history.
- Tagging/Labelling: Visible tags or labels on machinery ensure easy identification, particularly for communicating inspection status or warnings.
3. Risk Management Process
A systematic approach to risk management underpins effective plant safety. This involves:
- Hazard Identification: Proactively identify potential hazards associated with each item of plant (e.g., moving parts, pinch points, energy sources, hazardous substances).
- Risk Assessment: Analyse the likelihood and severity of potential injuries resulting from identified hazards.
- Control Implementation: Put in place control measures based on the hierarchy of controls:
- Elimination (remove the hazard entirely)
- Substitution (replace with a less hazardous option)
- Engineering controls (guards, interlocks, isolation systems)
- Administrative controls (procedures, training, signage)
- Personal Protective Equipment (PPE) (last line of defence)
- Monitoring and Review: Regularly evaluate the effectiveness of control measures and update as needed.
4. Consultation and Communication
The WHS Act mandates worker consultation on health and safety matters, including plant. This fosters better safety outcomes and a stronger safety culture. Here's how to achieve effective consultation:
- Open Communication: Establish channels for workers to raise concerns, report hazards, and suggest improvements.
- Involve Workers in Decisions: Include workers in risk assessments, developing safety procedures, and plant selection where possible.
- Safety Committees or Representatives: Facilitate worker input through formal structures
- Training and Information: Provide all workers with clear information about plant-related hazards and the safety measures in place.
5. Licensing and Competencies
Many types of high-risk plant require operators to hold specific licences issued by relevant state or territory authorities. Also essential are:
- High-Risk Work Licences: Licences demonstrating competency for operating cranes, forklifts, or certain types of earthmoving equipment.
- Proof of Competency: Documentation verifying training and experience on specific machinery items, even if a formal licence isn't required.
- Record Keeping: Maintain a register of licences and proof of competency, ensuring workers operating machinery are adequately qualified.
6. Operation and Use
Safe plant operation depends on clear procedures and adherence to safety rules, including:
- Manufacturer's Instructions: Always follow the manufacturer's instructions and safety guidelines.
- Pre-operational Checks: Implement pre-start checklists for each item of plant to identify faults or damage before use.
- Safe Work Procedures (SWPs): Develop detailed SWPs outlining safe operating methods, particularly for complex or high-risk plant.
- Exclusion Zones: Clearly mark areas around operating machinery to restrict access by unauthorised personnel.
- Traffic Management: Implement plans for workplaces where vehicles and pedestrians interact.
7. Maintenance, Inspection, and Repairs
Keeping plant in safe working condition is paramount to preventing incidents. This involves:
- Preventive Maintenance: Follow the manufacturer's recommended maintenance schedules, including regular servicing, lubrication, and replacement of worn parts.
- Inspections: Conduct pre-start checks and formal inspections by competent persons at specified intervals. Use checklists tailored to different machinery types.
- Maintenance Records: Document all maintenance, inspection, and repair work to track the condition of the equipment and identify any recurring issues.
- Qualified Personnel: Ensure qualified technicians or mechanics carries out repairs.
8. Lock Out Tag Out (LOTO)
LOTO procedures are vital to prevent machinery's accidental or unexpected start-up while it's being maintained, cleaned, or repaired. A typical LOTO process involves:
- Isolation: Disconnect the plant from all energy sources (electrical, hydraulic, pneumatic, stored energy like springs).
- Lock Out: Apply lockout devices (padlocks, tags) to prevent the reconnection of energy sources.
- Tag Out: Attach warning tags indicating the equipment is locked out and should not be operated.
- Test: Verify that the plant is isolated before commencing work.
- Release: Follow a structured process to remove lockout devices and restore energy sources only when it's safe.
9. Machine Guarding
Effective guards are essential safeguards against injuries caused by moving parts, pinch points, and other hazards. Consider:
- Types of Guards:
- Fixed guards (permanently attached)
- Interlocked guards (automatically stop the machine when opened)
- Adjustable guards
- Other types, like presence-sensing devices or safety barriers
- Suitability: Ensure guards are appropriate for the specific hazards and do not create new risks themselves.
- Situations Where Guarding May Not Be Possible: Certain maintenance or troubleshooting tasks might require the temporary removal of guards. In such cases, alternative strict safety controls should be implemented.
10. Emergency Procedures and Incident Management
Planning for the unexpected is crucial when working with plant. Ensure you have:
- Emergency Response Plan: Develop plans specific to potential plant-related incidents (fires, rollovers, contact with powerlines, etc.).
- Training and Drills: Ensure workers know the emergency procedures and participate in drills.
- Incident Reporting: Implement a system for reporting all incidents and near misses, no matter how minor.
- Thorough Investigations: Analyse incident data to identify root causes and prevent recurrence.
11. Decommissioning and Disposal
Safe disposal of plant is an often-overlooked aspect of the plant lifecycle. Key considerations include:
- Safe Shutdown: Isolate energy sources and remove any hazardous substances before decommissioning.
- Update Registers: Mark the equipment as decommissioned in your plant register.
- Environmental Considerations: Follow regulations regarding the disposal of hazardous materials (e.g., oils, batteries, chemicals).
- Safe Transportation and Handling: Use appropriate methods and equipment for moving and disposing of heavy or bulky machinery.
12. Audit and Compliance Review
Conducting audits provides valuable insights into the effectiveness of your plant safety management systems.
- Internal Audits: Regularly assess your systems against WHS regulations, the Code of Practice, and safety plans.
- External Audits: Consider periodic independent audits to gain an unbiased perspective.
- Tools and Checklists: Develop or utilise audit checklists to ensure a thorough and standardised evaluation.
13. Review and Continual Improvement
Plant safety is not a static process. To stay ahead of hazards and risks, focus on continual improvement:
- Incident Data Analysis: Regularly review incident and near-miss reports to identify patterns and areas where controls can be strengthened.
- Risk Assessment Updates: Revisit risk assessments as items of plant, work practices, or conditions change.
- Procedure Refinement: Refine safe work procedures based on worker feedback and observed best practices.
- Embracing Technology: Explore new technologies or tools that can enhance plant safety.
- Worker Input: Actively encourage workers to suggest improvements to safety processes.
The Value of a Plant Safety Management Plan
While the key areas discussed previously provide a solid safety foundation, a comprehensive Plant Safety Management Plan brings exceptional value by streamlining safety across the entire plant lifecycle within an organisation. Here's how:
- Centralised Knowledge and Processes: A well-structured plan consolidates all your plant safety knowledge in one place. This includes policies, procedures, risk assessments, licensing requirements, emergency plans, and maintenance records, ensuring consistency and ease of access.
- Support Documents for Easy Implementation: A robust plan incorporates crucial support documents, making it simple to implement effective safety practices. Examples include:
- Pre-purchase Checklists: Guide the evaluation of new equipment before the acquisition, ensuring safety is considered from the outset.
- Risk Assessment Forms: Provide a structured framework for identifying hazards, assessing risks, and implementing appropriate controls.
- Standard Operating Procedures (SOPs): Outline step-by-step instructions for safe plant operation, minimising variability and ensuring adherence to best practices.
- Pre-operational Checklists: Mandate inspections before each shift, helping to identify potential faults or damage.
- Lock Out Tag Out (LOTO) Procedures: Detail the steps to isolate energy sources and prevent unexpected start-up during maintenance.
- Incident/Near Miss Reporting Forms: Capture essential data for investigating incidents and identifying trends to drive improvement.
- Audit checklists: Facilitate thorough and consistent audits, ensuring compliance and revealing areas for optimisation.
- Lifecycle Management: A plan streamlines plant safety from the initial risk assessment at the pre-purchase stage through to safe disposal at the end of its useful life. It incorporates regular reviews and updates, ensuring the plan adapts as your organisation's needs evolve.
- Compliance Assurance: By aligning with the WHS Act, Regulations, and the Code of Practice, a plan significantly reduces the risk of non-compliance and the associated penalties, providing peace of mind.
- Enhanced Safety Culture: The very process of developing and communicating the plan fosters a more robust safety culture. Workers become active participants, and the shared knowledge and clear procedures promote a proactive approach to plant safety.
Managing plant safety can be complex and time-consuming. Simplify this challenge and achieve regulatory compliance with SafetyDocs by SafetyCulture's Plant Safety Management Plan.
Instead of building a system from scratch, this proven solution provides a centralised framework for all aspects of plant safety, from pre-purchase assessments to decommissioning. It includes essential forms, checklists, and templates, saving you valuable time and ensuring your plant safety strategy is effective and aligned with the best practices.
Author - Craig Cruickshank is the HSEQ Manager and Senior Technical Advisor at SafetyDocs by SafetyCulture.
Craig comes from a construction and environmental background, with experience in both the private and public sectors and is passionate about making health and safety information easy to find and understand for everyone.
Learn more about Craig's work on LinkedIn
Available for instant download and supplied in fully editable MS Word format for use in your business.
Please note that the above information is provided as a comment only and should not be relied on as professional, legal or financial advice.
Share This Article